Critical Steps to Achieve Long-Lasting Chemical Resistant Epoxy Floor Coatings in Vancouver
Vancouver, Canada - June 27, 2025 / Fraser Plus Epoxy Flooring /
If you think all epoxy floor coatings are created equal, you’re in for a surprise—and not the good kind. In Vancouver’s high-stakes commercial and industrial environments, where chemical spills are more a certainty than a possibility, the difference between a floor that shrugs off acids and one that crumbles under pressure comes down to three things: preparation, application, and maintenance.
At Fraser Plus Epoxy, we’ve turned this process into an art form, combining technical rigor with a dash of West Coast ingenuity. Here’s how we build floors that don’t just survive, but thrive, in the chemical jungle.
1. Surface Preparation: The Foundation of Chemical Resistance
Let’s get real: 80% of epoxy floor failures are traced back to poor surface prep. You can have the world’s best epoxy, but if you lay it on a dirty, damp, or oily slab, you’re just setting yourself up for a very expensive redo.
The Fraser Plus Epoxy Approach
1. Diamond Grinding: Forget acid etching or a quick sweep. We use industrial-grade diamond grinders to open up the concrete’s pores, creating a profile (CSP 2-3) that ensures maximum mechanical adhesion. Scientific assessments confirm that epoxy coatings deliver the highest pull-off adhesion strength and lowest water absorption rates among common floor coatings.
In Vancouver’s older buildings, we often encounter old sealers or paint—no match for our grinders.
This process doesn’t just clean the surface; it creates microscopic channels that allow the epoxy to physically grip the substrate, increasing the bond strength and preventing delamination even under heavy chemical exposure.
Recent research demonstrates that epoxy coatings maintain over 95% of their original strength after more than 15 years in demanding factory environments.
2. Shot Blasting: For large-scale industrial sites, shot blasting provides a uniform texture and removes stubborn contaminants. This is especially crucial for warehouses storing corrosive chemicals or heavy-duty manufacturing plants.
Shot blasting also exposes any hidden weaknesses in the slab, allowing us to address them before coating. The result? A surface that’s not only clean but also structurally sound and ready for the rigors of industrial life.
3. Moisture Mitigation: Vancouver’s humidity is legendary, and concrete is like a sponge. We use in-slab relative humidity probes (ASTM F2170) and calcium chloride tests to ensure moisture is below 4%. If not, we apply a moisture vapor barrier epoxy—because nothing ruins chemical resistance faster than hydrostatic pressure.
Moisture vapor transmission (MVT) can lead to blistering and bubbling, which compromise the integrity of the entire system. Our moisture mitigation solutions are specifically selected for Vancouver’s climate, ensuring long-term durability.
4. Crack and Joint Repair: All cracks and expansion joints are routed and filled with a flexible, chemical-resistant epoxy filler. This prevents future movement from telegraphing through the coating.
We also reinforce high-traffic areas with additional fiber-reinforced epoxy to handle dynamic loads and thermal cycling, which are common in Vancouver’s fluctuating temperatures.
5. Degreasing: Oil and grease are mortal enemies of epoxy. We use industrial degreasers and hot water extraction to ensure zero residue. In commercial garages and kitchens, we often perform multiple degreasing cycles, followed by a water break test to confirm the surface is truly clean.
Pro Tip: We once prepped a 10,000 sq. ft. food processing plant in Burnaby where previous coatings had failed twice in five years. After our prep and install, the client reported zero delamination or chemical staining after three years of heavy use. This underscores the importance of thorough, methodical preparation—cutting corners here is simply not an option.
2. Application
Application is where the “floor coating” becomes a “system.” Every layer has a job, and skipping steps is like building a house without a foundation.
Layer by Layer Breakdown
Epoxy Primer: We always start with a high-solids, penetrating primer. This locks down dust, seals pores, and prevents outgassing bubbles. Our go-to primer increases adhesion by up to 30% compared to unprimed surfaces. In Vancouver, where temperature and humidity can fluctuate, the right primer also acts as a buffer, accommodating minor substrate movement and preventing microcracking.
Body Coat: This is the muscle. For chemical resistance, we use 100% solids, cycloaliphatic epoxy—engineered to resist acids, caustics, and solvents. In Vancouver’s biotech labs, we routinely specify a 2–3mm thick body coat for maximum durability. The body coat is where we can tailor the formulation to your specific needs, whether you’re dealing with sulfuric acid in a battery plant or lactic acid in a dairy facility.
Broadcast Aggregate (Optional): For slip resistance and extra durability, we broadcast silica sand or aluminum oxide into the wet body coat. This is essential in areas prone to spills or heavy foot traffic. Aggregates also add thickness and impact resistance, making the floor suitable for forklift traffic and dropped tools—common in Vancouver’s busy warehouses.
Topcoat: We use a high-performance polyaspartic or urethane topcoat—formulated to resist UV, abrasion, and the harshest chemicals. In one Vancouver automotive facility, our topcoat withstood repeated exposure to brake fluid, gasoline, and battery acid with zero staining. The right topcoat also enhances color retention and gloss, keeping your floor looking sharp for years.
Environmental Controls
Application conditions are everything. We monitor temperature (ideally 18–25°C) and humidity (below 75%) with digital sensors. If the site’s too cold or damp, we bring in portable heaters and dehumidifiers. Rushed jobs in the wrong conditions? That’s how you get amine blush, soft spots, or poor chemical resistance.
Cure Time and Return to Service
Our fast-cure systems can be ready for light traffic in 12 hours and full chemical exposure in 72 hours. That means minimal downtime for your business—a critical factor for Vancouver’s 24/7 operations. For critical environments, we can even use rapid-cure polyaspartic systems that allow for same-day return to service.
Quality Control
Every Fraser Plus Epoxy project includes a detailed quality control checklist. We measure film thickness with digital gauges, check for pinholes with holiday detectors, and perform adhesion pull-off tests. We document every step, ensuring full traceability and accountability.
3. Maintenance of Epoxy Floor Coatings
You wouldn’t buy a Ferrari and never change the oil. The same logic applies to epoxy floor coatings. Proper maintenance can extend the life of your floor by 30% or more.
Daily and Weekly Routines
Sweep and Mop: Dust and grit act like sandpaper. Daily sweeping and weekly mopping with a pH-neutral cleaner prevent micro-scratches and preserve the topcoat. In high-traffic areas like Vancouver’s distribution centers, we recommend using microfiber mops to trap fine particles.
Immediate Spill Cleanup: Even the toughest floors have limits. Promptly clean up acids, solvents, or oils to avoid long-term damage. We provide clients with a chemical compatibility chart and recommended cleaning agents for their specific environment.
Periodic Deep Cleaning: For industrial clients, we recommend monthly auto-scrubbing with soft bristle pads. Avoid harsh chemicals that can degrade the topcoat. In food processing, quarterly steam cleaning may be appropriate, provided the floor has cooled to ambient temperature first.
Annual Inspection
Schedule a yearly inspection with Fraser Plus Epoxy. We’ll check for wear patterns, scratches, or early signs of delamination. Minor touch-ups now can save you a major overhaul later. We also offer maintenance packages that include scheduled resealing or topcoat refreshes, extending your floor’s lifespan and maintaining peak chemical resistance.
Long-Term Planning
For facilities with evolving needs—such as expanding production lines or changing chemical inventories—we offer consultation services to reassess your floor system annually. This proactive approach ensures your epoxy floor coatings remain fit for purpose, no matter how your business grows.
Why Chemical Resistance Matters in Vancouver, BC
Vancouver’s economy is powered by industries that demand chemical-resistant flooring—think biotech, food processing, automotive, and marine. According to BC Stats, the manufacturing sector alone employs over 180,000 people in Metro Vancouver, with many facilities requiring high-performance epoxy floor coatings.
Service Life: Properly maintained and installed epoxy floor coatings last 10–20 years in commercial and industrial settings. In some Vancouver warehouses, we’ve seen floors exceed 20 years with only minor touch-ups.
ROI: The average cost of epoxy floor failure and replacement can exceed $10 per square foot, not including lost productivity. Investing in quality upfront pays off—big time. A single day of downtime in a busy production facility can cost tens of thousands in lost revenue.
Safety: Chemical-resistant floors reduce slip hazards and contamination risks, protecting both workers and products. They also help facilities comply with WorkSafeBC regulations regarding workplace safety and hygiene.
Sustainability: Many of our epoxy systems are low-VOC and contribute to LEED certification, supporting Vancouver’s green building initiatives.
FAQs
1. How long do epoxy floor coatings last in industrial environments?
With proper preparation, application, and maintenance, epoxy floor coatings in Vancouver’s industrial settings typically last 10–20 years. High-traffic or chemical-heavy environments may require periodic touch-ups, but a full replacement is rarely needed within that timeframe.
2. Are epoxy floor coatings safe for food processing facilities?
Absolutely. Our epoxy floor coatings are formulated to meet CFIA and FDA standards for food safety. They’re seamless, non-porous, and easy to sanitize—perfect for Vancouver’s bustling food and beverage sector.
3. How resistant are epoxy floor coatings to acids and solvents?
Our industrial-grade epoxy systems are engineered to withstand exposure to most acids, alkalis, and solvents. For extreme environments (think sulfuric acid, xylene, or MEK), we specify novolac or polyaspartic topcoats for maximum resistance.
4. What is the installation downtime for epoxy floor coatings?
Most installations can be completed in 2–4 days, with light traffic allowed after 12–24 hours and full chemical exposure after 72 hours. We offer fast-cure systems for facilities that can’t afford extended downtime.
5. Can epoxy floor coatings be applied over old coatings or damaged concrete?
Yes, but only after thorough assessment and preparation. We remove failing coatings, repair damaged concrete, and ensure a sound substrate before applying the new system. Skipping these steps is a recipe for failure.
Final Thoughts: No Shortcuts, No Excuses
If you want epoxy floor coatings that shrug off chemical attacks and look good doing it, you need a partner who obsesses over the details. At Fraser Plus Epoxy, we bring decades of technical expertise, relentless quality control, and a Vancouver work ethic that doesn’t quit until the job’s perfect.
So, next time you’re staring down a concrete slab and dreaming of a floor that can take whatever your operation throws at it, remember: chemical resistance is earned, not given. And at Fraser Plus Epoxy, we earn it every single day.
Located at 2437 Dundas St, Fraser Plus Epoxy is just a short drive from anywhere in Vancouver. If you’re looking for expert epoxy floor coatings nearby, our team is only minutes away and ready to help.
Ready to upgrade your floors?
Visit them today to learn more about their epoxy floor coatings, request a quote, or schedule a site visit. Your floors—and your bottom line—will thank you.
Source Link: https://fraserplusepoxy.com/top-application-techniques-to-maximize-chemical-resistance-floor-coatings/
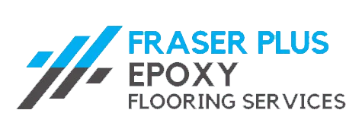
Contact Information:
Fraser Plus Epoxy Flooring
2437 dundas st. Vancouver BC V5K1 P5
Vancouver, BC V5K1 P5
Canada
Shaminder Sandhu
https://fraserplusepoxy.com/